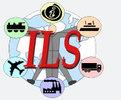
ILS 2012
Québec, Canada, 26 — 29 August 2012
ILS 2012
Québec, Canada, 26 — 29 August 2012

REGULAR SESSION: Production Scheduling and Sequencing I
Aug 27, 2012 10:30 AM – 12:00 PM
Location: VCH-2840
Chaired by Riad Aggoune
4 Presentations
-
10:30 AM - 10:52 AM
Scheduling on Three Identical Parallel Machines with a Single Operator and within the Free Changing Mode: A Geometrical Approach
This paper addresses the problem of scheduling a set of jobs on three identical parallel machines within the supervision of a single operator in order to minimize the makespan. In our context, the presence of an operator is necessary to operate the machines through a subset of a given modus operandi: the working modes. A working mode models the way the operator divides up his interventions between the machines, and consequently the ratio of productivity induced on each machine. Within this model, the processing times become variable as they depend on the working mode being utilized. A schedule is thus a partition of the jobs on the machines with the corresponding sequences, a subset of working modes along with their duration, and the order of their utilization. Based on the geometrical approach, we present mathematical properties to characterize an optimal solution when the interventions of the operator can change at any time.
-
10:52 AM - 11:14 AM
A Modified Shifting Bottleneck Procedure for Hoist Assignment and Sequencing in Surface Treatment Facilities
In this paper, we consider hoist scheduling problems with one (or several) hoist(s) in a job shop environment. The objective is to minimize the makespan. This kind of problem exists in surface treatment facilities and is NP-complete even for the simple cyclic case. It is represented by a disjunctive graph, which contains not only processing nodes but also transportation nodes. Arcs with respectively positive and negative values are introduced to model lower and upper bounds on processing times. Once all disjunctions are arbitrated, a solution is found. A solution is said to be feasible if the associated graph contains no positive cycle. To solve this graph, two heuristics coupled with a modified shifting bottleneck procedure with repair are proposed. The shifting bottleneck procedure is used for finding feasible sequences on resources. A simple repair is applied if the proposed sequence is not feasible. One heuristics is used to repair sequences of transportation tasks based on the original assignment. The other heuristics assigns and schedules transportation tasks. Various experiments on benchmarks show that our model and method are able to provide satisfying results.
-
11:14 AM - 11:36 AM
Production Planning of a Two-machine Manufacturing System with Production Dependent Failure Rates
A deteriorating production system consisting of two parallel machines with the production dependent failure rates of the machine is investigated in this paper. The machines produce one type of final products. The demand rate for the final commodity is constant and unmet demand is backlogged. The goal of the control problem is to find the production rates of both machines so as to minimize a long term average expected cost which penalizes both the presence of waiting customers and the inventory. In the proposed model, the production rate of the first machine (machine 1) is higher than the production rate of the second machine (machine 2). The failure rate of the machine 1 which is the main machine depends on its production rate. The failure rate of the second machine is constant. This paper proposes a stochastic dynamic programming formulation of the problem and derives the optimal production policies numerically. A numerical example is included and the sensitivity analyses of the optimal results with respect to the system parameters are also examined to illustrate the importance and effectiveness of the proposed methodology. In the near future, the proposed model will be extended to the reverse logistics.
-
11:36 AM - 11:58 AM
An Integrated Approach for Lot Sizing and Detailed Scheduling in Job-shops
In this paper, an improved integrated approach for solving the production planning and scheduling problem for multi-item multi-resource systems is proposed. Detailed capacity constraints are considered in the lot sizing model, thus guaranteeing feasible solutions. We use a Lagrangian heuristic to generate an optimal production plan for a fixed sequence of operations. A procedure proposing production plans with relaxed capacity constraints is combined with a smoothing procedure which modifies these production plans to satisfy the capacity constraints. Then, a sequence improvement method is performed to feed the Lagrangian heuristic with different sequences. A Tabu search is used to guide the selection of sequences.