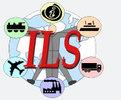
ILS 2012
Québec, Canada, 26 — 29 August 2012
ILS 2012
Québec, Canada, 26 — 29 August 2012

INDUSTRIAL SESSION: Strategic Management of Inventory at the Enterprise Level I
Aug 29, 2012 10:30 AM – 12:00 PM
Location: VCH-2870
Chaired by James A. Rappold
4 Presentations
-
10:30 AM - 10:52 AM
Error Reduction in an (r,Q) Normal Demand Inventory System
In practice inventory models are still very often based upon normal distribution although more accurate representations exist. For the performance measures such as average inventory, average backorders, ready rate, fill rate and orderline service level further simplifications are also applied without knowing the risks linked to it. We analyze the maximum and average errors on these performance measures when a Poisson or compound Poisson leadtime demand is approximated with a normal distribution. Conditions are defined to allow the use of simplified equations and corrections are made. The modifications are very simple allowing a quick implementation in practice and existing models.
-
10:52 AM - 11:14 AM
Predictions for Future Order Statistics under Parametric Uncertainty with Applications to Inventory Control Problems
A large number of problems in production planning and scheduling, location, transportation, finance, and engineering design require that decisions be made in the presence of uncertainty. Most models, which are used for solving these problems, are developed under the assumptions that the parameter values of the models are known with certainty. When these models are applied to solve real-world problems, the parameters are estimated and then treated as if they were the true values. The risk associated with using estimates rather than the true parameters is called estimation risk and is often ignored. In this paper, we consider statistical prediction problems which are invariant with respect to a certain group of transformations. If a given decision problem admits a sufficient statistic, it is well known that the class of invariant rules based on the sufficient statistic is essentially complete (under some assumptions) in the class of all invariant rules. If, in this case, there exists an optimal invariant rule among invariant rules based on sufficient statistic, it is optimal among all invariant rules. The primary purpose of this paper is to introduce the idea of cumulative customer demand in inventory control problems to deal with the order statistics from the underlying distribution. This idea allows one to use the invariant embedding technique to improve statistical decisions for inventory control problems under parametric uncertainty. We discuss the statistical decisions for the exponential distribution.
-
11:14 AM - 11:36 AM
Sales and Operations Planning as an Integrating Enabler for a Joint-Venture
Sales and operations planning (S&OP) is a process used to meet strategic goals through the reconciliation of tactical supply and demand plans (monthly or quarterly targets) with operational execution (daily, weekly production and inventory control and allocation). However, the S&OP process has organizational benefits that extend beyond functional integration. We introduce a case of a joint business venture between two North American firms and describe how S&OP was a necessary condition of the joint venture success and how it contributed to long-term cohesion of the business at all levels. We discuss the competitive and operational forces that shaped the decision to pursue S&OP and describe the process of implementation as well as the key functions, capabilities, roles and metrics used to ensure the success of the business. The success of the joint venture hinged upon an S&OP process that was characterized by strong, effective leadership, shared performance metrics, an integrated information technology (IT) system that allows real-time access to shared data, a disciplined business process that establishes an analysis and decision cadence, and a decision support tool that allows management to make decisions and execute them quickly utilizing all operational and strategic information in the business environment. We contribute to the sparse but growing academic literature on S&OP by providing a case of how a joint venture used the S&OP process to integrate the business functions of two organizations to achieve operational and financial success.
-
11:36 AM - 11:58 AM
A Stochastic Inventory Model for the Stock versus Non-Stock Decision
The most fundamental decision in inventory management is whether or not to stock a particular item. Despite its importance, the preponderance of the literature on inventory systems is concerned with how much to order and when to order which assume the stocking decision has been made. In this research we examine an inventory stocking decision model that is based upon an item’s demand history. In this model every item must earn its way into the catalogue of stocked items by receiving a given number of demands over a specified time period and will likewise be de-stocked and taken out of the catalogue (or burned) if it receives fewer than a given number of demands over a specified time period. We show the stability of such a policy and discuss implications for its use by firms that compete on product assortment.