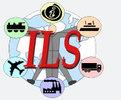
ILS 2012
Québec, Canada, 26 — 29 August 2012
ILS 2012
Québec, Canada, 26 — 29 August 2012

REGULAR SESSION: Maintenance
Aug 28, 2012 04:30 PM – 06:00 PM
Location: VCH-2840
Chaired by Fouad Riane
3 Presentations
-
04:30 PM - 05:00 PM
A Profit Assessment Model for Equipment Sold under Warranty and Subject to Random Generation of Environmental Damage
One of the major interests of the green supply chain management is the concept of green productivity, which is focused on environment, quality, and profitability. To face these challenges, manufacturers and consumers need to establish efficient maintenance policies for their products in order to meet environmental legislations requirements. This paper develops a model to determine the profit generated by a service contract for a certain type of equipment sold with a warranty and which can randomly shift to a polluting state releasing hazardous substances or over consuming energy causing direct or indirect damage to the environment. Such undesirable state can only be known through inspec-tion. The customer and the manufacturer agree that during the warranty period, the manufacturer inspects the equip-ment according to a specified schedule and supports the costs incurred for equipment inspections and replacement if pollution is detected. After the expiration of the warranty, inspections and replacements are performed by the manufac-turer and billed to the customer. Moreover, penalties related to pollution are always supported by the manufacturer. An analytical model taking into account the commitments of both parties is developed. An algorithm is also presented to generate the inspection instants given the costs structure and the probability distribution associated with the time to shift to the polluting state. With the advent of increasing environmental concerns and business models arguing for tech-no-environmental implication of suppliers towards their customers, the proposed decision model may be relevant and very useful.
-
05:00 PM - 05:30 PM
Joint Redundancy and Imperfect Preventive Maintenance Optimization
This paper presents two algorithms based on Harmony Search algorithm (HS) and Genetic algorithm (GA)to solve a joint redundancy and imperfect preventive maintenance planning optimization problem for series-parallel multi-state degraded systems. Non identical multi-state components can be used in parallel to improve the system availability by providing redundancy in subsystems. Multiple component choices are available on the market for each subsystem. The status of each component is considered to degrade with use. The objective is to determine jointly the minimal-cost series-parallel system structure and the appropriate preventive maintenance actions, subject to a availability constraint. System availability is defined as the ability to satisfy consumer demand that is represented as a piecewise cumulative load curve. A procedure is used, based on Markov processes and universal moment generating function, to evaluate the multi-state system availability and the cost function. The two algorithms are compared through two numerical examples.
-
05:30 PM - 06:00 PM
An Integrated Model for Production, Maintenance and Quality
In this paper, three main aspects are integrated in the same model: production, maintenance, and quality. We are given a set of products that must be produced in lots on a production system during a specified finite planning horizon. The objective is to determine an integrated lot-sizing and preventive maintenance strategy of the system that will minimize the sum of preventive maintenance costs, inspection costs, production costs, setup costs, inventory holding costs, backorder costs, and the costs of producing nonconforming items, while satisfying the demand for all products over the entire horizon. We model the production system as a multi-state system with multi-state and s-independent components. Each component represents a machine for which the status is considered to degrade with use, and these degradations may lead to the production of nonconforming products. In addition, a machine can fail randomly from any operational state and can be repaired. This repair action brings the machine to its previous operational state without affecting its failure rate (i.e. minimal repair). The used preventive maintenance policy suggests also that planned preventive maintenance can be performed on each machine. During each period, machines are inspected,
and imperfect preventive maintenance activities are performed to reduce the ages of the
machines, proportional to the preventive maintenance level. A machine is stopped either when the inspection reveals that it is producing nonconforming products, or at the end of the current period. Once stopped, a machine is restored to the as good as new conditions to be ready for the next production period. An evaluation method is proposed to calculate the production rates of conforming and nonconforming items. We finally discuss the assumptions under which the model can reformulated to be solved by comparing the results of several multi-period multi-product capacitated lotsizing problems.