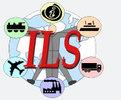
ILS 2012
Québec, Canada, 26 — 29 August 2012
ILS 2012
Québec, Canada, 26 — 29 August 2012

THEMATIC SESSION: Optimization of Production and Assembly Lines Design III
Aug 28, 2012 10:30 AM – 12:00 PM
Location: VCH-2840
Chaired by Vincent Giard
4 Presentations
-
10:30 AM - 10:52 AM
A Framework for Comparison of CONWIP with G-MaxWIP and CWIPL Production Control Mechanisms
Production control mechanisms are used to control WIP in a production line. The way in which performance is measured, and the methodology used to compare the performance of various production mechanisms, will influence the conclusions on the superiority of such mechanisms. We present a unified framework to compare the performance of three mechanisms: Constant Work in Process (CONWIP), Gated MaxWIP (G-MaxWIP), and Critical WIP Loops (CWIPL). We use a simulation model based on the Production Authorization Card (PAC) mechanism to estimate performance. Two measures are used to evaluate system performance: throughput, and average WIP in the line on or after the first machine. The goal is to simultaneously maximize throughput and minimize WIP. We develop optimal policy curves (or trade-off curves) to select highlight optimal policies for each mechanism, and use these curves to compare the performance of these different mechanisms. We show that G-MaxWIP does not always outperform CONWIP, and CWIPL does not outperform either G-MaxWIP or CONWIP.
-
10:52 AM - 11:14 AM
An Algorithm to Optimize Packaging Sizes at CooperPharma Maroc
In this paper, we study the problem of optimizing packaging sizes based on a real-life problem. We develop a (hierarchical) mathematical model that optimizes the packaging sizes by taking into consideration the packaging material cost and the picking cost. The picking cost results from the difference between the customer order size and an integer multiple of the box size. We solve the mathematical model for a range of different parameter settings and derive interesting managerial insights.
-
11:14 AM - 11:36 AM
Solving Buffers Sizing Problems on Assembly Lines Using Multiobjective Genetic Algorithms
This paper is focused on solving multiobjective buffers sizing problems on assembly lines. The multiobjective side is due to the fact that we are trying to optimize two criteria simultaneously: the minimization of the total buffers size and the maximization of the throughput rate of the line. Our contribution in this work is to propose a new multiobjective metaheuristic based on coupling the Strength Pareto Evolutionary Algorithm (SPEA-II) with a fuzzy logic controller (FLC) to solve the problem. In fact, coupling this metaheuristic with FLC allows a dynamic and an improved setting of the two main genetic algorithms which are the crossover and the mutation probability. To prove the efficiency of this approach, named FLC-archive, we have carried out several experimental results to compare the numerical results with those obtained with another efficient approach that we have already developed. The latter is based on applying the Lorenz dominance relationship with an SPEA-II algorithm instead of the Pareto dominance relationship. The algorithm was named L-archive. Both FLC-archive and L-archive are compared to the classical SPEA-II algorithm.
-
11:36 AM - 11:58 AM
A Simulation-based Optimization Approach for an Integrated Production and Quality Control Model
This article presents an integrated production and quality control model for an unreliable and imperfect batch manufacturing system. The production is controlled by a hedging point policy, while, the quality control is performed by a lot-by-lot double acceptance sampling plan by attributes. The decision variables of this model are the production lot sizing and the hedging level. The purpose of this work is to develop and validate a simulation model to fairly represent the dynamic and stochastic aspects of the system under study. Then, a simulation optimization approach based on the response surface methodology is used to optimize the decision variables when the failure and repair times and the percentage of nonconforming items produced follow general probability distributions.