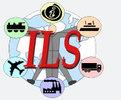
ILS 2012
Québec, Canada, 26 — 29 August 2012
ILS 2012
Québec, Canada, 26 — 29 August 2012

THEMATIC SESSION: Reconfigurable Manufacturing Systems: Design and Operational Strategies
Aug 28, 2012 10:30 AM – 12:00 PM
Location: VCH-2830
Chaired by Jean-Pierre Kenné
4 Presentations
-
10:30 AM - 10:52 AM
Ecodesign of New Products: A Methodological Comparison
Along with the increase of environmental concern throughout the second half of the 20th century and the ecological awareness brought by it, the preoccupation with production, development and eventually disposal of products grew, not only among multinationals companies and governments, but also among gradually more informed consumers. This article analyses the interaction between traditional product development process and ecologically concerned product development methodologies evaluating possible opportunities and improvements from the combination of its best practices finally providing an optimized eco-development model.
-
10:52 AM - 11:14 AM
Simultaneous Control of Production, Repair/Replacement and Preventive Maintenance of Deteriorating Manufacturing Systems
This paper presents results of simultaneously control of production and a special case of integration of the preventive maintenance into the repair/replacement policy of a failure-prone system. The machine of the considered system exhibits increasing failure intensity and increasing repair times. The status of the system is deemed to degrade with production and repair activities. The machine manufactures one type of product, and when a breakdown occurs, either a repair or a replacement action is chosen. A replacement action renews the machine, while a repair action brings it to a degraded operational state, with the next repair time increasing as the number of repairs increases as well. To reduce the failure rate and subsequent repair times following a failure, there is an incentive to perform preventive maintenance on the machine before failure. The preventive maintenance action is considered in order to improve the reliability of the machine, thereby reducing the amount of disruptions caused by machine failures. The decision variables of the control problem are the production rate, the preventive maintenance rate and the repair/replacement switching policy upon machine failure. The objective of the study is to find the decision variables that minimize the overall cost, including repair, replacement, preventive maintenance, inventory holding and backlog costs, over an infinite planning horizon. The study considers the fact that machine repair activities depend on the repair history, and a Semi-Markov Decision Process (SMDP) is used to describe the dynamics of the system. The optimality conditions was developed using the stochastic dynamic programming approach, with a numerical example to illustrate the utility of the proposed approach, and a sensitivity analysis to confirm the structure of the control policy obtained.
-
11:14 AM - 11:36 AM
Role of Configurator for Mass Customization Program in the Fashion Apparel Industry
Mass customization offers the opportunity to meet, even surpass, customers’ expectations; this being true whether one aims for pure mass customization (one individual-one garment) or merely a highly precise market segmentation. Yet to reach this objective, one needs to acquire and manage a knowledge base of consumers’ needs and preferences. In the fashion & clothing industry, mass customization is not generally well understood or implemented due to difficulties related to measurements, pattern adaptation, and inflexible manufacturing processes. The objective of our research is to (1) identify the fundamental variables and data necessary to produce custom-made clothing, (2) to develop a configurator based on such data, and (3) to enable the efficient transmission of configurator generated information to computerized production systems. For producers to make the most of mass customization they need to better understand what can be done in terms of clothing personalization and mass customization. They also must formulate an appropriate strategy as to how they wish to approach mass customization in order to develop a competitive advantage.
-
11:36 AM - 11:58 AM
Optimal Unlimited Free-Replacement Warranty Policy Using a Mixture of New and Reconditioned Components
The total lifecycle of a given product or component is extended through the process of remanufacturing. This second life given to the reconditioned part is attractive for the manufacturer and consumer both from an economical and environmental perspective. These reconditioned products can be used as replacement parts in honouring warranties. This paper considers the case where a mixture of new and reconditioned components are used to carry out replacements upon failure. A mathematical model is developed to determine the proportion of new and reconditioned components to be used. Numerical optimization is used to compute the optimal warranty and production parameters which maximize the total profit.