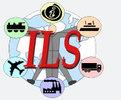
ILS 2012
Québec, Canada, 26 — 29 August 2012
ILS 2012
Québec, Canada, 26 — 29 August 2012

THEMATIC SESSION: Optimization of Production and Assembly Lines Design I
Aug 27, 2012 02:30 PM – 04:00 PM
Location: VCH-2840
Chaired by Lionel Amodeo
4 Presentations
-
02:30 PM - 02:52 PM
Linking Data-Driven Risk Analysis and Discrete Event Simulation for Supply Chain Strategic Decisions
In today’s manufacturing global environment, world-class companies are aiming to standardize their operations in which their product is built using the same assembly “formula” across all their sites. For this, companies are aiming towards a profitable partnership with their supply chain that provides flexibility and is fast to the market changes. Most risks associated with product industrialization are due to hidden supply chain costs that if business owners knew ahead of time, they could make better decisions when it comes to globalizing products. This paper attempts to show how discrete event simulation can help mitigate these ‘hidden cost’ during the product rationalization process and the optimal mix of actions to make decisions based on the true costs that are linked to the strategy.
-
02:52 PM - 03:14 PM
Application of an Artificial Immune Algorithm to Solve a Robotic Assembly Lines Balancing Problem of Type E
In this paper, an industrial application of an artificial immune algorithm for solving a robotic assembly line balancing is proposed in order to maximize the lines efficiency. The idea is to implement the developed method in a real case system to manage the functioning of pick and place robotic assembly lines which request a short execution time. For this raison, we are unable to apply an exact method that requires a large execution time. This is the main advantage of our method compared to exact methods.We aim to find the suitable assembling tasks and components of products in order to guide each robot in the process of gripping products. Numerical results show that the different algorithms perform efficiently for the tested instances in a reasonable computational time.
-
03:14 PM - 03:36 PM
Optimizing Item Trips from a Production Line to Trucks
This paper addresses the problems of minimizing the number of trips in order to load into trucks items coming from a production line. The transportation device used can only take at the same time a limited number of consecutive items going to the same destination. Although related to the games of Tetris, this problem is different to make a generalization of known complexity results. A dynamic programming algorithm is first presented to solve this problem. Although of exponential running time, the experimental results show that this algorithm outperforms by far the integer linear programming presented in Baptist et al. (2011). In the second step, we show that when discarding two constraints related to the capacity of the transportation device and the size of the window through which the items become visible in the production line, the problem is solved in polynomial time through a repeated application (though polynomially bounded) of the shortest path algorithm.
-
03:36 PM - 03:58 PM
The Impact of Variable Operator Walking Distances on the Decision to Supply in Bulk or in Kits
In the automotive industry, a high diversity of vehicles is assembled on mixed-model assembly lines. To allow for production, many different variant parts need to be supplied to these lines and stored at the border of line. Moreover, because parts are often large, the border of line can become enormous. This in turn leads to large walking distances and inefficient production. To free up some space at the line, kitting is introduced as an alternative materials supply method next to line stocking, i.e. feeding the line in bulk. This paper proposes a mathematical cost model which assigns all of the parts to one of both methods. The model explicitly takes into account variable operator walking distances at the line and in the kitting area. Results of the model are discussed and guidelines for logistics engineers are provided in the form of hypotheses.